

The Making of an Eighteenth Century French Writing Table
After the selection of first and secondary woods for the construction of the desk the wood is blocked into rough forms, which form the basic rough assemblage. This is shown in the following photographs. The leg and carcass pieces will be cut, carved and assembled from these hefty blocks. They are then clearly the desk form in whichonstructed into the fine unadorned understructure of you are now able to clearly see the sillouette of the piece.


Eighteenth century French furniture has several attributes, which make it technically superb. The first is a painstaking attention to exactness. All the individual pieces are carefully matched for quality and symmetry. This attention belies the fact that the work is hand done. The second is a superb technical skill, modern and sophisticated even by our contemporary standards. Many pieces were constructed to serve multiple purposes. The mechanical workings of the furniture may include hidden drawers with springs, double table tops or ‘invalid tables’ allowing the first top, complete with short legs, to be lifted off and used as a bed tray, combination writing and toilette tables which exposed either a leather writing surface or a pop-up vanity mirror with spring loaded drawers custom fitted with matched necessities in porcelain, cut crystal, silver and/or silver-gilt, writing tables which hid gaming compartments and the pieces for chess, backgammon or cards and those with overlapping sliding tops (as exemplified in this table which has a pull out leather inset for writing when in use as a desk, but which hidden away shows the beautiful marquetry top and may then be used as a tea table.
This type of quality was not accomplished without sacrifice. France worked with its various trades in Guilds. Each Guild oversaw one aspect of the various different construction techniques of a typical piece of furniture. Therefore, the base construction and design were delegated to one craftsman’s shop, the marquetry veneers to another, the porcelain insets and gilt bronze mounts to yet others; each master concentrating on his one craft and producing that individual piece with great pride to the highest possible degree of perfection. There were of course distinctions in quality, pieces destined for the king and queen and court had significantly greater detail than those designed for the home of a well to do bourgeoisie merchant. Yet, even with these variants of class quality remained a primary tenant. It is testament to this quality that this furniture is every bit as sought after today as it was when it first reached the somewhat.
The marchand –merciers were the dealers and somewhat the equivalent of today’s interior design firms. These savvy style makers helped promote luxury goods and were responsible for innovations, such as Chinese porcelain mounted in gilt bronze and the exquisite toiletry sets which made there way into the dressing tables of the upper classes.

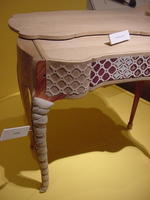


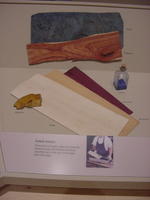
The final step was the joining of the bronzes, gilt bronzes or ormolu mounts. These pieces designed, produced and provided by a separate Guild are certainly a familiar trademark of French furniture. No other country ever achieved the magnificent pefection of the French Guilds. The mounts were executed from cartoons and then generally rendered in the lost wax method. If the furniture was not executed on commission the bronzes were generally not gilded until a client purchased the piece from inventory, requesting the costly process.
This very brief description of the production of this desk is wholly inadequate. It is, perhaps, enough to garner a very slight overview of the methods and practices of the great French ébénistes, but certainly does them little real justice. It has hopefully wet your appetite. I recommend reading all the texts you can to fully understand this complex artisan society and the complexity of the craftsmanship. Despite the Guilds there were many artisans who made a living outside the lawful framework and still produced some amazing pieces. Additionally, this short article describes the work of only the Parisian high-end makers and does not allow you any understanding of the many exciting variances of the regional provincial makers using local woods, motifs and techniques. These country French pieces are as highly sought after today as their city cousins. Go explore!
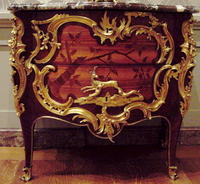

A very fine text is produced by the J. Paul Getty Foundation. It is
'French furniture Makers, The Art of the Ebéniste from Louis XIV to the Révolution',
authored by Alexandre Pradere. Expensive and worth every ‘livres’!
'French furniture Makers, The Art of the Ebéniste from Louis XIV to the Révolution',
authored by Alexandre Pradere. Expensive and worth every ‘livres’!
No comments:
Post a Comment